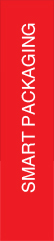
IN MOLD LABELS

In Mold labels consist of a substrate, normally made of BOPP, which is deposited in the mould for injection-moulded, blow-moulded or thermoformed plastic packaging at the time the packaging is shaped, and so becomes incorporated into the packaging's outer surface. We currently find this product applied in tubs and containers for ice-cream, butter and margarine, yoghurt products, salads and cheeses.
The in-mould label becomes part of the very packaging to which it is applied, to the extent that the human eye does not see it as a conventional label. This has a considerable aesthetic benefit, which should be added to the leap in printing quality that the offset system enables us to offer and the environmental benefits offered by the product, because recycling is easier when packaging and label are made of the same material.
By combining the moulding and decorative processes, clients can gain in terms of cost efficiency.
Other advantages of the process:
The in-mould label becomes part of the very packaging to which it is applied, to the extent that the human eye does not see it as a conventional label. This has a considerable aesthetic benefit, which should be added to the leap in printing quality that the offset system enables us to offer and the environmental benefits offered by the product, because recycling is easier when packaging and label are made of the same material.
By combining the moulding and decorative processes, clients can gain in terms of cost efficiency.
Other advantages of the process:
- Production of already-labelled packaging in a single step, with technology that is revolutionary in the plastic-container sector.
- Perfect adhesion to the container, including on curved surfaces.
- Label cannot be tampered with or removed, preventing fakes.
- Injection moulding (PP and PE)
- Blow-moulding (high- and low-density PE and PP, particularly for bottles)
- Thermoforming (PP)